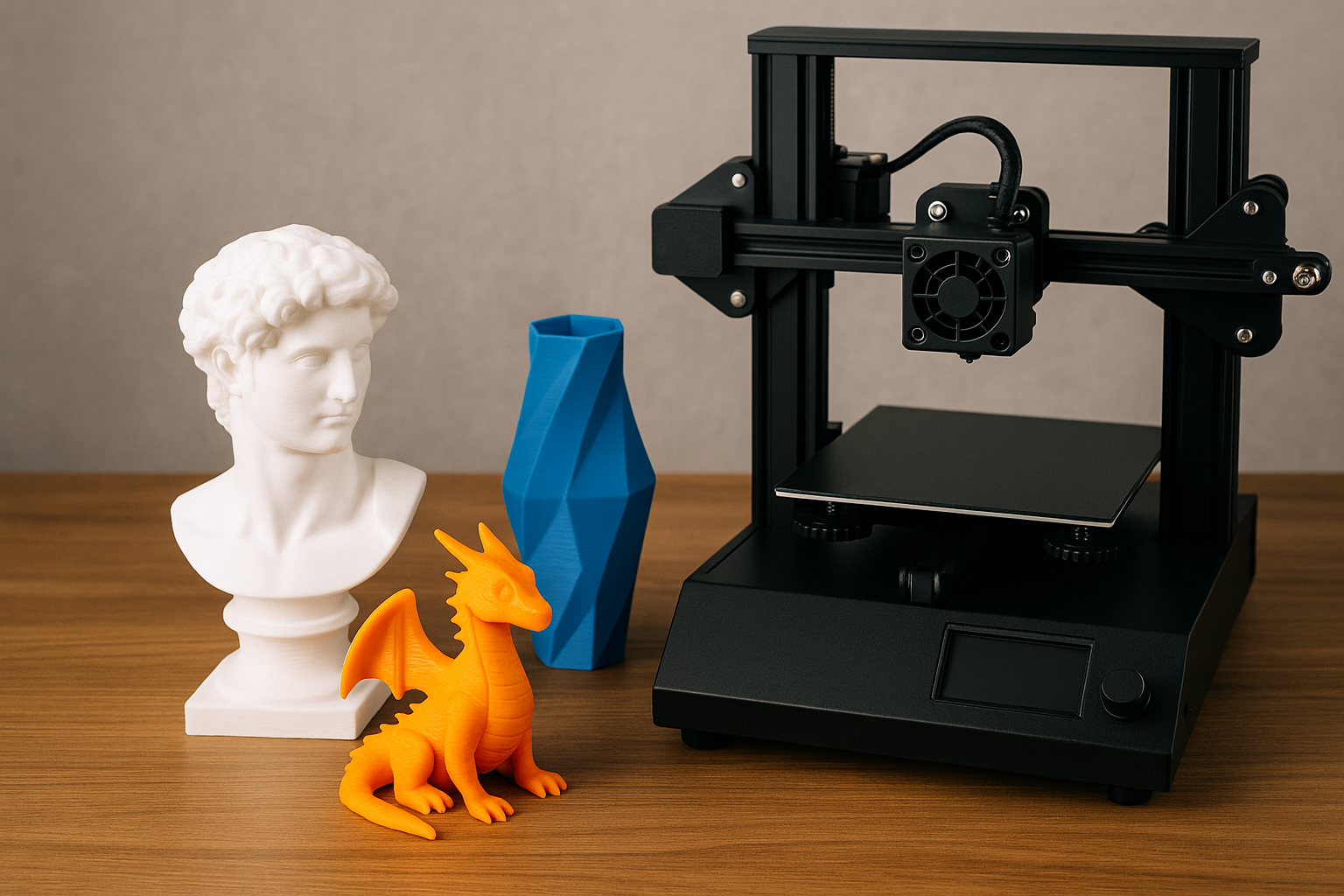
3D Printing for Hobbyists: Applications, Trends & Getting Started
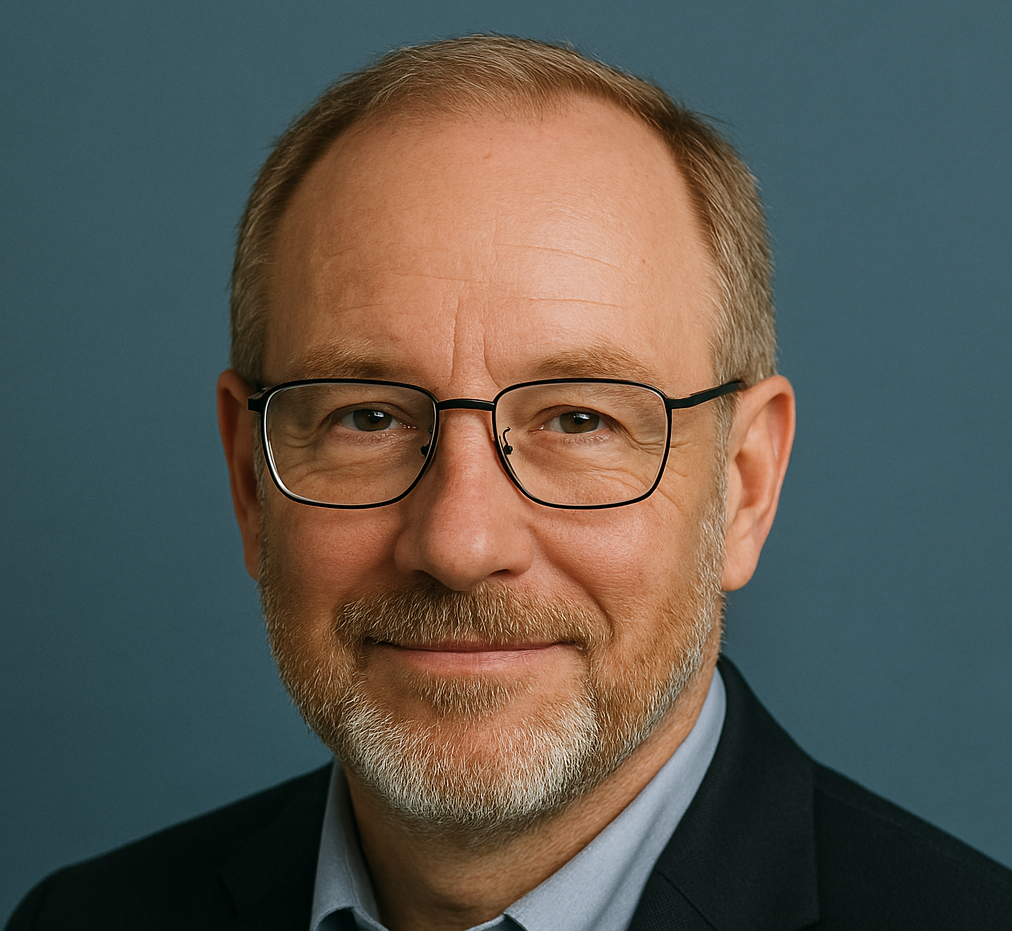
Exploring the world of 3D printing for the first time can feel a bit like stepping into a science fiction story. The idea that you can dream up a design, click a button, and watch it come to life right on your desk still amazes me, even after years of being around the technology. What was once reserved for high-tech labs and giant corporations is now easily within reach of anyone with a curious mind and a few hundred bucks. Whether you’re a tinkerer looking to fix things around the house, a gamer wanting to print miniatures, or just someone who loves learning new creative skills, 3D printing opens up a crazy amount of possibilities.
When I first dipped my toes into the hobby, I honestly thought it would be a lot harder than it was. Sure, there’s a bit of a learning curve: anything worth doing usually is, but the huge community of makers, endless free resources, and rapid improvements in printers and materials make it way easier and more fun than you might expect. It’s one of those hobbies where you can start simple, like printing a phone stand, and before you know it, you’re designing your own custom parts or building full cosplay outfits. The best part? You don’t need a PhD in engineering or a million-dollar machine to get started. You just need a little patience, a sense of adventure, and maybe a bit of duct tape for good measure.
So let's walk through the practical side of 3D printing for hobbyists: what you can make, how the technology has grown, what gear to start with, and what’s really possible as an amateur. Whether you’re curious about printing a missing piece for your coffee grinder or dreaming of building a working robot, you’ll find that 3D printing has a place for you. Let’s get into it.
Practical Applications of 3D Printing for Hobbyists
Hobbyists use 3D printing in a wide variety of creative and practical ways. Some of the most popular applications include:
- Cosplay Props & Costumes: The customizability of 3D printing is a perfect fit for cosplay. Enthusiasts print detailed helmets, armor pieces, weapons, and masks that can be sanded and painted for realism. In fact, some makers have even turned their cosplay prop hobby into businesses thanks to 3D printing (e.g. prop-maker Jordan Duncan’s success with Henchmen Props). Large costume pieces are often printed in sections and then assembled, which allows creating full-size armor or props at home.
- Scale Models & Miniatures: Model makers and gamers print everything from tabletop miniatures and figurines to scale models of vehicles or buildings. Resin 3D printers (SLA/DLP) are especially popular for miniatures, since they can achieve extremely high resolution and fine details – SLA prints have smooth surfaces and crisp details unrivaled by FDM, with layer resolutions as fine as ~25 microns. This lets hobbyists produce professional-quality figurines for games like D&D or Warhammer, or highly detailed model kits, at home.
- Tools, Jigs & Practical Gadgets: Many hobbyists use their printers to solve everyday problems or organize their workshops. It’s common to print custom tool holders, brackets, and jigs, as well as replacement parts for equipment. For example, community members have shared prints like battery holders, tool organizers, project boxes, and spice rack assemblies designed to fit better than off-the-shelf options. One user printed a spice rack with 3D printed brackets and ASA filament for heat resistance. It maximized storage where no commercial product would fit. Another popular project is printing upgrades for the printer itself (knobs, cable guides, etc.), reflecting the self-reinforcing nature of this hobby.
- Home Repair & Replacement Parts: 3D printing shines for making one-off parts to fix things around the house. Hobbyists print knobs, clips, handles, and other broken plastic parts to repair appliances or furniture. As one maker noted to me recently, “the MOST useful [thing] was a door handle – I use it every day.” Others have printed things like a ramp to help a robot vacuum over a threshold (instead of buying a premade one), or custom hooks and brackets. Being able to “will [a needed part] into existence” on demand is a huge perk of owning a 3D printer.
- Art, Decorations & DIY Projects: Beyond utilitarian items, hobbyists also create decorative art pieces, figurines, and gifts. From vases and planters to cosplay display pieces and holiday decorations, 3D printing allows endless personalization. Artistic makers experiment with multi-color printing or post-processing (sanding, painting, hydro-dipping) to produce display-worthy pieces. For example, printing unique Christmas ornaments or figurines can be both fun and, as one user joked, “works wonders to pacify the wife” with custom décor. The range of projects is vast. If you can design or download a 3D model of it, you can likely print it.
These examples only scratch the surface. Whether it’s building custom RC car parts, drone frames, musical instrument pieces, or educational models, hobbyist 3D printers are being used in virtually every creative domain.
Broader Developments and Trends in 3D Printing
Beyond personal projects, the 3D printing field as a whole is evolving rapidly. Key developments and trends include:
- Increasing Industrial Adoption: What started as a prototyping technology is now becoming a legitimate manufacturing tool. As of 2024–2025, industry experts note that 3D printing has moved “beyond prototyping to mass production”, especially in high-value sectors like aerospace, defense, automotive, and medical devices. Companies are integrating additive manufacturing into production lines for end-use parts, not just one-off prototypes. For example, manufacturers print custom jigs, fixtures, and even final components (like automotive brackets or medical implants) on-demand. This trend is enabled by improved printer reliability, larger machines, and multi-laser systems that can print faster and at scale. In short, 3D printing is graduating from a “fast friend” for prototyping to an integral part of the family in production.
- Mid-Range and High-Performance Machines: Along with industrial use, there’s a push toward mid-tier printers that bridge the gap between hobbyist and industrial. In the past, one either bought a cheap kit or an extremely expensive industrial machine. Now a “mid-range market” is emerging, with prosumer printers offering high-quality output at more accessible prices. This includes advanced filament printers with enclosed chambers, auto-calibration, and even multiple toolheads, as well as affordable metal and resin systems aimed at small businesses. The result is that quality is improving across the board. Today’s $500 printer can achieve results that a few years ago might’ve required a $5,000 machine.
- Materials Innovation: The palette of materials for 3D printing keeps expanding. For plastics, new filament formulations (like PLA+, impact-resistant PETG, flexibles, carbon-fiber or wood-filled composites, etc.) allow hobbyists and industry alike to create parts with tailored properties. In industrial spheres, there’s intense development of advanced materials: fiber-reinforced thermoplastics, high-temp polymers (PEEK, Ultem) for aerospace, and a range of metal powders and photopolymer resins.
Even at the hobby level, engineering-grade materials like Nylon and polycarbonate are accessible with some tuning, even cheap printers can use Nylon or PC filament to produce strong, functional parts. Moreover, new printing processes like pellet extrusion (using plastic pellets instead of filament) are emerging to reduce material costs for large prints. Researchers are also exploring bioprinting materials, concrete (for construction printing), and even food pastes – pushing 3D printing into new domains. - Sustainability Focus: As 3D printing becomes more widespread, there’s growing attention to its environmental impact. Encouragingly, many in the industry are making sustainability a priority. Companies are investing in recyclable and bio-based materials, spool-less filament systems (to cut down on plastic waste from spools), and more energy-efficient processes. A vision for “sustainable additive manufacturing” has been articulated by researchers, calling for a “circular” approach where printer design, material supply chains, and end-of-life recycling are all optimized for sustainability. For example, some initiatives collect and recycle failed prints and scrap filament into new filament.
Others have introduced PLA recycling programs and environmentally friendly materials (like PLA made from corn starch, or PETG made from recycled bottles). While 3D printing isn’t inherently green (producing plastic waste and consuming energy), the hope is that through design for reuse and material innovation, it can support a more eco-friendly manufacturing ecosystem aligned with global sustainability goals. - Digital Supply Chains & Decentralization: Another trend is the concept of “print on demand” reducing the need for inventory. Instead of mass-manufacturing a part and shipping it worldwide, companies are starting to keep digital files and print parts locally when needed. This digital supply chain model, already embraced by spare parts services, got a boost amid recent global supply chain disruptions.
We see more platforms for sharing 3D printable designs (with secure digital rights management for commercial files) and more networks of printing services. In the consumer space, this is mirrored by the huge repositories of user-created models (Thingiverse, Printables, Thangs, etc.) where makers around the world share and download designs. It’s never been easier to find or distribute a 3D model, meaning anyone with a printer has on-demand access to millions of parts and products they could print.
In summary, 3D printing is maturing: it’s becoming faster, more capable, and more integrated into both industry and everyday making. At the same time, the community is conscious of making it more sustainable and accessible. These trends from the industrial side often trickle down to hobbyists in the form of better printers and materials over time.
Comparison of Popular 3D Printing Technologies
There are several distinct 3D printing technologies available, each with its own strengths and weaknesses. The most common ones for hobbyists are FDM, SLA, and SLS. The table below provides an overview and comparison:
Technology | How It Works (Material) | Pros | Cons | Typical Costs (Hobby Use) |
---|---|---|---|---|
FDM (Fused Deposition Modeling) – filament extrusion | Melts and extrudes thermoplastic filament through a nozzle, depositing layers that harden (common materials: PLA, ABS, PETG, etc.). |
- Most common and least expensive 3D printing technology - Wide range of printers and materials available - Easy to use; good for larger parts - Strong parts suitable for functional prototypes |
- Visible layer lines, lower surface detail compared to resin - Requires support structures for overhangs - Some materials can warp or emit fumes - Tolerances and fine features limited by nozzle size |
Printers: ~$200–$800 for hobby-class machines Material: ~$20–$40 per 1 kg filament spool |
SLA (Stereolithography) – resin curing | Uses a UV laser or screen to cure liquid photopolymer resin layer by layer into hardened plastic. |
- Highest resolution and accuracy - Smooth surfaces ideal for painting and display - Resin formulations available for various properties |
- Post-processing required (washing and UV curing) - Resin is messy and can be toxic before curing - Smaller build volumes - Materials are pricier per volume |
Printers: ~$250–$600 for hobby models Resin: ~$35–$80 per liter |
SLS (Selective Laser Sintering) – powder sintering | A laser fuses particles of powder (usually nylon plastic powder) together layer by layer, building a solid part in a bed of powder. |
- No supports required - Strong, functional parts in nylon - Can produce complex, interlocking geometries |
- Very expensive machines - Powder handling is messy - Surface finish is granular and rough - Limited material availability at hobby scale |
Printers: ~$5,000 and up (rare for home use) Material: Nylon powder ~$100+/kg |
Other technologies: Beyond these three, there are others like DLP (very similar to SLA, using a projector), MJF (HP’s Multi Jet Fusion, similar to SLS but with binding agents), Binder Jetting (for full-color sandstone or metal powder with binder), and FDM variants like multi-material jetting. However, FDM, SLA, and (to a lesser extent) SLS cover the vast majority of hobby and desktop 3D printing usage. Each has unique advantages, so makers choose the technology that fits their project’s needs (for example, FDM for a large functional bracket, versus SLA for a tiny detailed figurine).
Getting Started: How Amateurs Can Begin 3D Printing
So, how can a beginner dive into 3D printing? Here we outline the essentials: choosing an entry-level printer, getting materials and software, understanding costs, and finding learning resources.
Recommended Entry-Level 3D Printers
There are dozens of options on the market, but a few 3D printers consistently stand out for beginners in terms of ease-of-use, community support, and value:
- Creality Ender 3 (V3 SE and variants) – The Ender 3 series is famous as a budget-friendly FDM printer line. The newest Ender 3 V3 SE model offers modern features (auto bed leveling, dual Z-axis, etc.) at a very low price. It’s a “bedslinger” style (open frame, moving bed) printer with a decent build volume (~220×220×250 mm). Pros: huge user community, tons of mods and tutorials, and a low cost to get started. Cons: usually requires some assembly and occasional tweaking to get perfect prints, but it’s a great learning platform. The Ender 3 is often recommended as a first printer for those on a tight budget.
- Prusa i3 MK4 or Prusa Mini+ – Prusa Research’s printers are a bit more expensive but known for reliability and top-notch print quality out of the box. The Original Prusa i3 MK4 (the successor to the award-winning MK3S) is an FDM machine. They come with features like automatic bed leveling, a magnetic spring-steel build plate, and well-tuned firmware. Prusa printers are supported by an extensive community and great official documentation. They’re open source and upgradable. Many beginners who want a smooth, no-fuss experience (and are willing to invest a bit more) choose Prusa as a long-term workhorse printer.
- Bambu Lab A1 Mini (and P1P/P1S) – Bambu Lab is a newer company making waves for integrating advanced features at a consumer level. The A1 Mini (released 2024) has been called “the ideal beginner 3D printer” by reviewers. It’s a compact FDM printer that comes fully assembled and calibrated, with enclosed sides for safety, automatic calibration, and even the option to add a multi-color filament feeder (AMS). Bambu’s slightly larger P1S and flagship X1 series are also praised for their speed and ease of use. These printers emphasize smart automation. They can self-level, detect errors, and print fast. For a newcomer who wants high-tech convenience (and is less price-sensitive), Bambu Lab printers are a strong choice in 2025.
- Anycubic & Elegoo (Budget Resin Printers) – If your goal is to print miniatures or very detailed models, an entry-level resin SLA printer might be appealing. The Elegoo Mars and Anycubic Photon series are popular LCD-based resin printers. For example, the Elegoo Mars 3 offers high resolution (down to 35 micron XY pixels) and a modest build area (good for minis, jewelry, small parts). These printers come mostly assembled; beginners can get them working with minimal setup. Resin printing has a learning curve regarding safety (resin is toxic until cured) and post-processing, but the print quality can be stunning for the price. Many hobbyists actually start with an FDM machine for general use and later add a resin printer for detailed projects.
Tip: When choosing a first printer, consider what you want to make the most. For cosplay props or larger functional items – go FDM. For tiny display models or intricate parts – consider starting with resin. Also factor in that FDM is generally cheaper and less messy to work with initially. Fortunately, the entry cost for great printers has come down dramatically – you can get a very capable 3D printer for only a few hundred dollars today.
Essential Materials and Software
Once you have a printer, you’ll need materials to print and software to prepare your designs:
- Filament Materials (for FDM): Beginners are almost always advised to start with PLA filament. PLA (Polylactic Acid) is a biodegradable plastic that is easy to print – it melts at low temperatures, doesn’t require a heated enclosure, and has low warping/shrinkage. It’s very beginner-friendly and comes in dozens of colors. PETG (a glycol-modified polyester) is another common filament; it’s a bit tougher and more heat-resistant than PLA and only slightly harder to print. ABS is a classic plastic (used in Lego bricks) but it’s tricky for home printers – it requires higher temperatures and tends to warp or crack without an enclosure; it also emits fumes (not dangerous but unpleasant), so experts often suggest avoiding ABS on your first printer unless you have a specific need for it. Many other filaments exist – flexible TPU for rubbery parts, Nylon for very strong functional parts, polycarbonate, wood-filled PLA, etc. – but those are better attempted after you get the basics down. A 1 kg spool of PLA filament is typically ~$20–$30 and can yield many prints.
- Resins (for SLA/DLP): Resin printers use liquid photopolymer resin. For beginners, a standard ABS-like resin is a good starting point. It’s a general-purpose resin that balances strength and detail. Resins are sold in 0.5–1 liter bottles, typically $30–$50 per liter for standard types. There are also specialty resins (tough resin, flexible resin, castable resin for jewelry, etc.) at higher costs. Keep in mind resin handling requires nitrile gloves, and you’ll need isopropyl alcohol for cleaning prints. The cost per print can still be low. A small miniature might only use a few cents of resin – but factor in the cost of post-processing supplies (gloves, alcohol, maybe a UV curing light if not included). Importantly, always use resin in a well-ventilated area and follow safety guidelines.
- Slicing Software: To go from a 3D model to a printable file, you need a slicer. The slicer “slices” the 3D model into the hundreds of 2D layers that the printer will produce, and generates the toolpath (G-code instructions for FDM, or images for each layer in SLA). Popular slicers include Ultimaker Cura (free, open-source), PrusaSlicer (free, open-source), and vendor-specific ones like Bambu Studio or Elegoo’s ChituBox for resin. These programs let you position the model, choose settings like layer thickness, infill density, support generation, etc., then export the file for printing. They are quite powerful; for example, you can specify different infills or supports, and preview how the printer will build each layer. The good news: slicer software is almost always free. Cura and PrusaSlicer are highly recommended and have profiles pre-configured for many common printers, making it easier for beginners to get started.
- 3D Design Software: Not all hobbyists design their own models – many rely on downloading existing models, but if you want to create or modify designs, there are great free tools available. For absolute beginners, Tinkercad is an easy online CAD tool with a gentle learning curve (great for simple functional designs). For more advanced modeling, Autodesk Fusion 360 is a powerful CAD software that is free for personal hobby use.
Others use Blender (free, open-source) for artistic and organic modeling. These software tools allow you to design anything from a phone stand to a cosplay helmet from scratch. Once designed, you export to an STL file for slicing. Additionally, 3D scanning apps or devices can help capture real-world objects to print, though that’s a more niche approach. Overall, there’s no shortage of software. The main point is you do not need to buy expensive software to succeed in hobby 3D printing.
Finally, you’ll also want some basic tools: a set of hex keys (often included with printers), flush cutters (for snipping filament or supports), a scraper or palette knife to remove prints from the bed, and some sandpaper or files for smoothing edges. If you have an FDM printer, blue painter’s tape or glue stick is sometimes used on the print bed for better adhesion (depending on the bed surface). None of these are very expensive. Many toolkits for 3D printing are available under $20 and come with these essentials.
Typical Costs to Budget For
One of the great things about desktop 3D printing is how affordable it has become. Here’s a breakdown of typical costs for a hobbyist setup:
- Printer Hardware: As noted, a good entry-level FDM printer can cost anywhere from around $200 up to $500 for a very solid machine. Resin printers are in a similar range (around $250–$600 for most). If you opt for a higher-end or larger format printer, you might spend $800–$1500, but this is not necessary for beginners. Many popular starter printers (Ender 3, Prusa Mini, Elegoo Mars, etc.) are in the $200–$400 range. Do budget for possible upgrades or mods – for example, you might later buy an all-metal hotend ($50) to print higher-temp materials, or an enclosure ($100) if you want to print ABS safely. These can be done over time as needed.
- Materials: Filament is very cheap per part. A 1 kg spool of PLA at ~$25 can produce dozens of mid-sized objects; the cost of plastic in a single print is often just cents to a few dollars. Resin, while more expensive per liter, still yields a low per-part cost (a tabletop mini might use less than $0.50 of resin). However, with resin you’ll also regularly buy isopropyl alcohol and perhaps replacement FEP film for the tank. For FDM, besides filament you might occasionally need to replace build surface sheets ($10–$20) or nozzles ($1–$5 each, very cheap). Overall, the consumable costs are modest, especially compared to many other hobbies. One All3DP guide noted that for hobby use, “the cost of materials is relatively similar for FDM and SLA” on the whole: meaning neither will break the bank for casual printing.
- Other Supplies: Don’t forget to account for ancillary supplies like tools (if not included), spare parts, and electricity. 3D printers do use power, but a small desktop printer only draws a few dozen to few hundred watts when running. A long 10-hour print might consume on the order of 1–2 kWh (perhaps ~$0.10–$0.20 of electricity in the US). It’s not zero, but unless you’re running printers 24/7, the energy cost isn’t a big factor at hobby scale. If you plan to paint your prints, factor in primer, paints, and brushes. Altogether, a beginner might comfortably start 3D printing with an initial investment of around $300 (for a basic printer and some filament) and then perhaps $20–$50 on assorted tools and materials which is a relatively low entry cost for the capabilities you gain.
Key Learning Resources and Communities
One of the best aspects of the 3D printing hobby is the vibrant, sharing community and wealth of learning resources available. As a beginner, you’ll never be alone. There are countless tutorials, forums, and groups to help you. Here are some of the top resources to tap into:
- Online Communities (Forums, Subreddits, Discord): The r/3Dprinting subreddit on Reddit is one of the largest communities, with over 3 million members as of 2025. It’s a place where makers of all skill levels share their prints, ask questions, and help each other troubleshoot issues. There are also more specialized subreddits (e.g. r/functionalprint for purely practical prints, r/PrintedMinis for miniature painting and printing, etc.). Outside of Reddit, communities like the Prusa Forums and various Facebook groups (for specific printer brands or interests) are active. Joining these communities is great for quick help. You can search past threads or ask for advice and typically someone has encountered the same problem or project. The camaraderie and knowledge-sharing in the maker community is a huge asset for learners.
- YouTube Tutorials & Channels: Many people find video tutorials very helpful for learning 3D printing techniques. Some highly regarded YouTube channels in the 3D printing space include Thomas Sanladerer (deep dives into printing tech and how-tos), CNC Kitchen (Stefan explores material strength and print optimization with a scientific approach), Maker’s Muse (Angus covers creative ideas and printer reviews/tips), and CHEP – Filament Friday (Chuck Hellebuyck gives practical tips and quick upgrades). These channels produce content ranging from beginner basics (e.g. first prints, leveling the bed, slicing settings explained) to advanced projects (like printing functional gears or multi-material prints). Many beginners follow along with “how to set up your new printer” videos as they unbox their machine. The visual guidance can be reassuring. Additionally, channels like 3D Printing Nerd and Uncle Jessy cover lots of hands-on projects and printer reviews which can be both educational and motivating.
- Online Courses & Guides: For a more structured learning, there are free online courses and guides. For example, Coursera offers a “3D Printing Revolution” course and even a multi-part specialization on 3D printing that covers fundamentals and applications. These courses can give you a broad overview of the technology and its uses in a few weeks of study. Another excellent resource is the Free Beginner’s Guide on 3D Printing Industry’s website (3DPI). It’s a comprehensive text covering all basics of 3D printing technologies, materials, and workflows. Many 3D printer manufacturers also have good tutorials: Ultimaker’s website has a lot of educational material; Prusa Research provides an extensive Knowledge Base and even a printed handbook with their printers. And of course, books like 3D Printing Book: A Beginner’s Guide to Design, Develop, and Innovate (by Oliver Tucker) or 3D printing without prior knowledge: 7 days to your first 3D print (Become an Engineer Without Prior Knowledge) by Benjamin Spahic can serve as offline references. Whether you prefer video, interactive courses, or reading, there’s a learning resource suited to you.
- Model Repositories and Project Sites: A big part of learning is actually printing things, and you don’t have to design everything yourself. Websites like Thingiverse, Printables.com (Prusa’s repository), MyMiniFactory, and Thangs host millions of free 3D models uploaded by the community. As a beginner, you can download models that interest you; whether it’s a Benchy (the famous tugboat benchmark print), a phone stand, or a baby Yoda figurine and print them to practice. Printing existing designs helps you learn how to fine-tune settings for different shapes without the added complexity of design. Many people also learn by examining print files others share (seeing how they oriented a model or used supports). Once you gain confidence, you might remix or customize models (Thingiverse allows uploading “remixes”). Engaging with these project sites can spark ideas and accelerate your learning by example.
In short, you have a whole ecosystem of support. Don’t hesitate to leverage it when you face a challenge, chances are someone else has posted the solution online. The 3D printing community is generally welcoming and excited to see new people join. From Reddit Q&As to YouTube tutorials and beyond, you’ll find answers to almost any question that comes up.
What Can Hobbyists Achieve? (Quality, Complexity & Project Possibilities)
Modern hobbyist 3D printers are surprisingly capable. While they have some limits, the gap between consumer and industrial capabilities has been closing. Here’s a realistic look at what amateurs can do in terms of print quality, complexity of designs, and types of projects:
- Print Quality and Detail: With a well-tuned FDM printer, amateurs can routinely achieve layer heights of 0.1–0.2 mm, producing very smooth results. Fine nozzles (0.2 mm) can push detail even further (at the cost of speed). Resin printers can go down to 0.05 mm layers or less, capturing details that are essentially indistinguishable from injection-molded or cast parts to the naked eye. This means hobbyists printing minis or figurines can get professional-shop quality on their desktop.
Of course, achieving the best quality takes calibration; dialing in settings to avoid artifacts like ringing or z-wobble. But thanks to profiles and community settings sharing, even beginners can get excellent results after a bit of tweaking. The main quality limitation of FDM is visible layer lines on smooth curves – however, these can be mitigated by post-processing. It’s common for hobbyists to sand and paint prints to get a flawless finish (especially for cosplay or display pieces). In fact, painting is a great equalizer: a $200 printer can produce a cosplay prop that, after sanding, priming, and painting, looks like a movie prop. Dimensional accuracy on well-calibrated hobby machines is often within ±0.1–0.2 mm, plenty good for fitting most prints together or making functional parts like enclosures. In summary, amateurs today can produce very high-quality prints; perhaps not always as perfect as a $100k industrial machine, but close enough that for most purposes you wouldn’t notice a difference. - Functional Strength: Beyond looks, hobbyists can make parts that serve real functional purposes. PLA, while easy to print, is somewhat brittle, which is fine for many uses (like a headphone stand or model) but it might crack under stress or heat. However, materials like PETG, ABS, ASA, Nylon, or polycarbonate have much better mechanical properties. Using an under-$500 printer, people have made things like replacement gears, drone frames, camera mounts, custom tools and more, that hold up in everyday use. For truly load-bearing parts, hobbyists might use fiber-filled filaments (e.g. carbon fiber PETG) which significantly boost stiffness. As one Reddit user put it, for “high quality functional parts, FDM is the way to go” and even tough materials can be used on cheap printers with some tweaking.
It’s now common to see 3D-printed pieces in DIY electronics projects, robotics, and home improvements. That said, plastic prints do have limits: they’re not as strong as solid metal, so one shouldn’t expect a printed part to replace a steel one in high-stress scenarios (e.g. you wouldn’t 3D print a car axle at home). But for medium-duty applications and especially custom-fit solutions, hobby prints can be plenty strong. There are also post-print techniques like annealing (baking a PLA part to strengthen it) or coating a print in epoxy for durability, which some use to enhance performance. In realistic terms, a hobbyist can produce a replacement plastic knob or a bike accessory that works just as well as a store-bought item – the only caveat being to choose the right material and design with the material’s strengths in mind. - Complex Geometry and Assembly: One of 3D printing’s superpowers is creating shapes that are impossible to make by traditional methods. Hobbyists leverage this to print very complex objects – such as spheres within spheres, links of a chain interlocked, or elaborate lattice structures – often in one go. FDM printers do require support for overhanging features, which adds a bit of complexity (supports must be removed and can leave marks), but slicers generate these automatically and they usually break away cleanly. SLA printers also require supports for many models, but they preserve fine details exceptionally well.
With careful planning, amateurs can design print-in-place mechanisms like gears, hinges, even working locks, all printed as a single assembly with moving parts. SLS technology (if accessible via a service) can produce even more complex interlocking parts with no supports needed. For larger projects, as mentioned, people slice models into sections that fit their printer and then glue or bolt them together. It’s how life-size costume armor or large sculptures are tackled. The ability to manufacture complexity for free means even a novice can print, say, a model of a DNA double helix or a replica of a famous statue with all its undercuts. The bottom line: amateurs are limited more by imagination than geometry, if you can model it (or find the model), you can likely print it, though you may have to strategize supports or assembly for very large or intricate pieces. - Multi-Material and Multi-Color Printing: Consumer printers are increasingly offering multi-material capabilities. While your basic $300 printer usually has a single extruder (one material at a time), there are options like the Prusa MMU (Multi-Material Upgrade) or Bambu Lab’s AMS (Automatic Material System) that feed multiple filaments and can create multi-color prints. This allows hobbyists to print objects with different colored sections or even different material types in one print (for example, a soft grip section and a hard body in a tool handle). However, multi-material printing adds complexity (oozing and alignment issues to manage), so many amateurs opt to print parts separately and assemble or simply paint after printing.
As of 2025, true full-color 3D printing at the consumer level is still rare. One of the only somewhat affordable full-color options was the XYZprinting da Vinci Color (which injects ink into filament), but it’s not widely adopted. For now, most hobby prints are single-color by default, but the creative use of filament swaps (changing filament at certain layer heights to create color bands) or painting can achieve the desired aesthetics. Notably, for resin, full-color printing is essentially not available in consumer models (it exists in industrial machines and some experimental setups). To summarize, amateurs can do multi-color/multi-material prints with additional hardware, but many find it simpler to print in one material and then post-process (assemble or paint) to get multi-colored results. With that said, the emergence of machines like Bambu’s, which make multicolor more plug-and-play, means we’ll likely see even hobby prints in multiple colors more often going forward. - Scale of Projects: Hobby printers come in various sizes. A typical desktop printer might handle objects around 200–300 mm (8–12 inches) in each dimension. This is sufficient for a vast number of projects (e.g. figurines, household items, gadget enclosures). For bigger ambitions, there are larger format home printers (CR-10, Anycubic Kobra Max, etc.) that can print up to 400 mm or more. People have printed small furniture, full cosplay helmets, and large architectural models on such machines. Really huge prints (beyond ~0.5 m) often require either outsourcing to a commercial service or printing in parts.
The good news is assembling parts is straightforward (common methods include using superglue, epoxy, or even designing dovetail joints or screw holes into the model). Using these techniques, hobbyists have made full Iron Man suits, large costume swords, and even functional kayaks and boats assembled from many printed sections! So realistically, with patience, an amateur could print something as large as a car bumper by printing it in pieces. There are also examples of community projects where multiple people each print a section of a big design (like a huge sculpture) and then combine them. In essence, the printable size is a limitation of one part, but not of the final project if you’re clever.
Conclusion
The capabilities of amateur 3D printing are broad and continually expanding. Today’s hobbyist can create high-quality, custom objects that are functional and intricate – from a tiny, detailed miniature figurine to a large, multi-piece cosplay armor set or a replacement part for a home appliance. The learning curve exists, but as thousands of makers have shown, it’s entirely feasible to reach a level where your prints look professional. As printers and materials continue to improve, the bar will only rise. We’re at a point where the question is less “Can a hobbyist make this?” and more “How can they best make it?” – because given the right tools and knowledge, the possibilities are vast. 3D printing empowers amateurs to become manufacturers and inventors on a small scale, turning digital ideas into real objects at will, and that capability is truly exciting for any hobbyist or creative maker.
You May Also Like
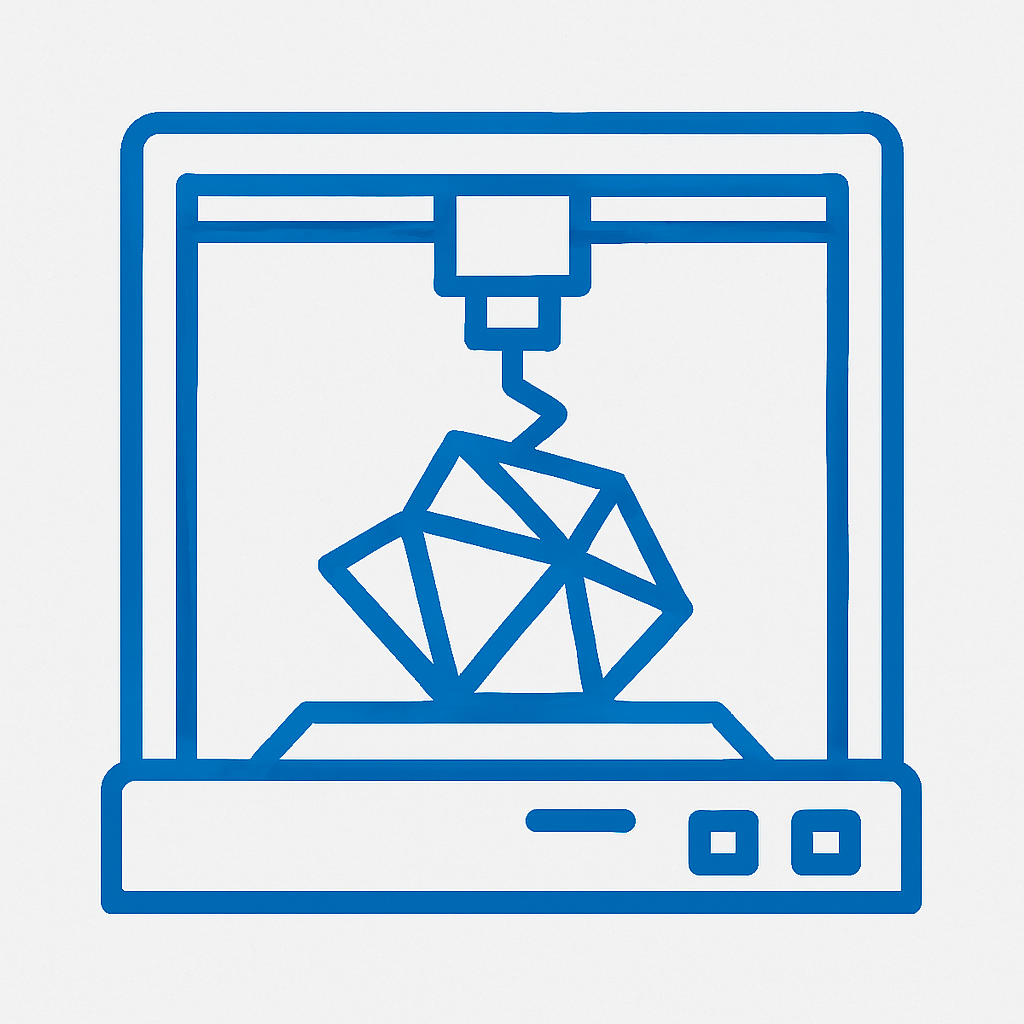
The Future of 3D Printing: Where Innovation Is Headed Next
3D printing is evolving from a niche innovation into a powerful force reshaping industries, sustainability, and the way we design our future.
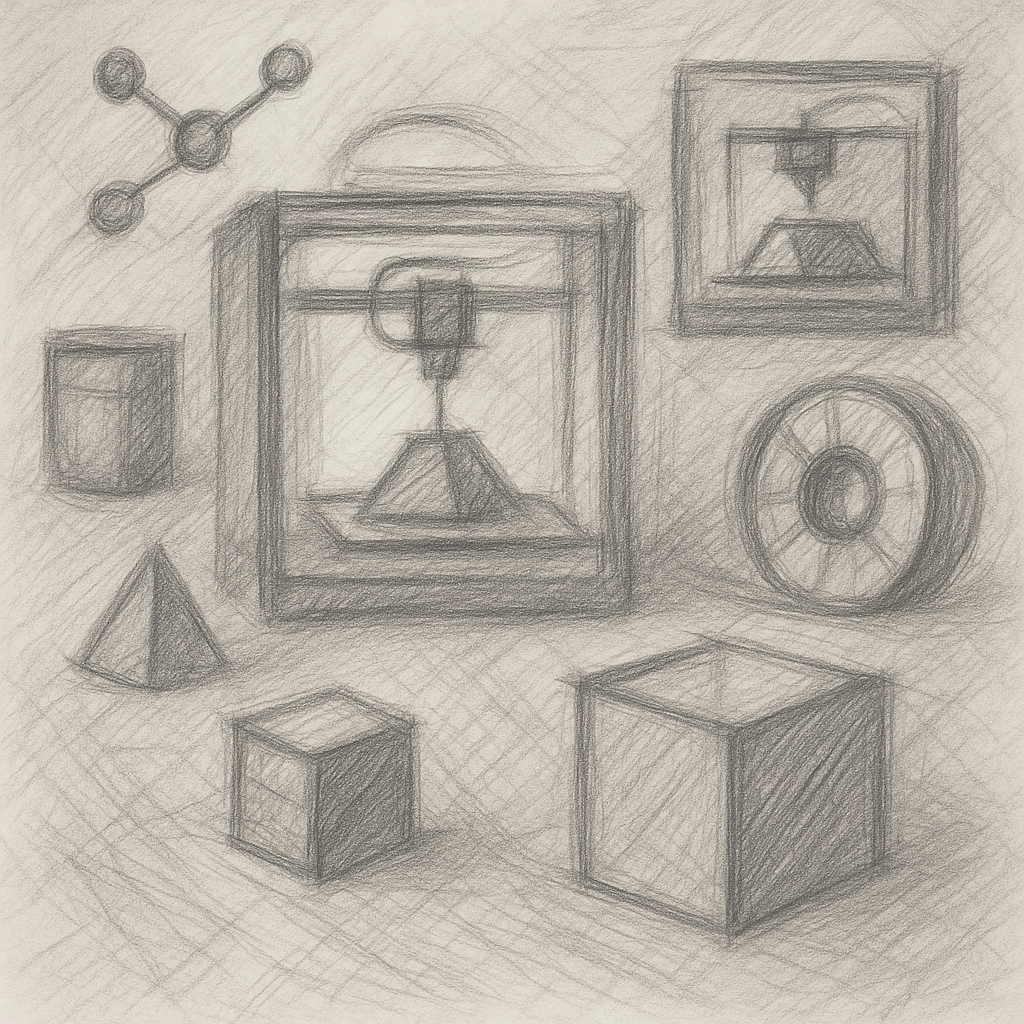
The Best 3D Printers in 2025: A Complete Buyer’s Guide
Discover the top 3D printers of 2025, from budget-friendly speedsters to professional-grade powerhouses, each chosen to match different needs and skill levels.